La NASA sviluppa una lega 1000 volte più resistente per applicazioni aerospaziali
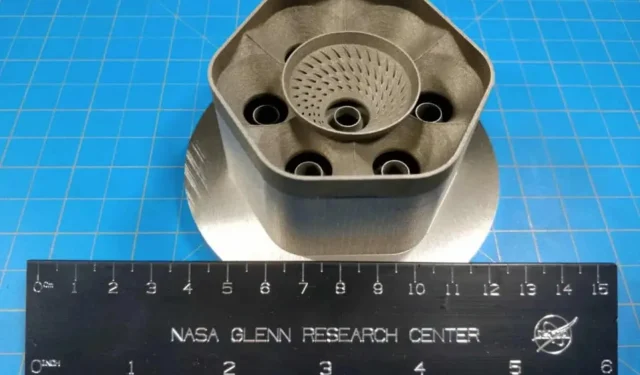
La NASA svela la sua lega GRX-810, una creazione promettente ed estremamente resistente.
La conquista dello spazio è un numero incredibile di sfide tecniche in una varietà di aree. Uno di questi riguarda i materiali utilizzati. La NASA, l’agenzia spaziale statunitense, lavora giorno dopo giorno per creare i materiali di domani, sia per fabbricare i suoi razzi che per equipaggiare i suoi astronauti. Oggi l’agenzia presenta la promettente lega GRX-810 .
La NASA svela la sua lega GRX-810
La lega GRX-810 può resistere a temperature fino a 1100°C e potrebbe essere un componente importante nella progettazione e produzione dei futuri motori a razzo. Questa lega stampata in 3D è rinforzata con una dispersione uniforme di nano-ossidi, il che significa che la sua struttura è molto complessa, ottenuta posizionando diversi tipi di particelle in punti specifici della griglia del materiale. Questi materiali sono incredibilmente resistenti e ideali per le condizioni molto difficili dello spazio o vicino allo spazio.
Creazione estremamente tenace molto promettente
La NASA spiega che GRX-180 ha una resistenza 1.000 volte superiore in tali condizioni rispetto alle leghe esistenti attualmente utilizzate nel settore. Questa durabilità e il processo ottimizzato dei componenti di stampa 3D potrebbero avere un enorme impatto sul costo del volo spaziale.
Si noti che “1000 volte più durevole” non significa “1000 volte più stabile”. Ciò significa che la vita del materiale è più lunga perché è più resistente al calore e alle sollecitazioni. Allo stesso tempo, GRX-810 è due volte più forte delle leghe odierne quando si tratta di rompersi. La NASA spiega anche che questa lega è anche 3,5 volte più flessibile delle attuali alternative, il che è impressionante.
La NASA ha utilizzato simulazioni termodinamiche numeriche per sviluppare la composizione di questa lega e afferma che la ricetta ottimale è stata trovata dopo sole 30 simulazioni.
Oltre ad essere utilizzato in ambito aerospaziale, questo tipo di materiale, e più in generale nella scienza dei materiali, sta iniziando ad essere utilizzato nei prodotti di consumo, in particolare nelle automobili o nei nostri gadget elettronici. E col tempo non farà che peggiorare. La capacità di stampare parti estremamente precise, unita allo sviluppo del materiale ideale per le esigenze, apre molte porte in termini di design.
Lascia un commento